导读:汽车发动机前罩壳零件油道较多且相互独立,各油道之间不得因缩孔造成贯穿渗透导致泄漏。在压铸模设计时,针对各油道内部致密性要求比较高的部位,通过抽芯加挤压实现局部挤压,并在压铸机中增加挤压报警和插芯喷涂,完成局部挤压动作配合压铸机开合模,实现局部挤压联动插芯喷涂功能,减少铸件内部缩孔,提高其致密性,满足前罩壳产品试密封要求。
汽车制造业的发展,对降低能耗的要求越来越高,汽车零部件逐步由铸铁件向铝压铸件转化,产品向轻量化、高集成和高性能化方向发展,且出现了越来越多结构复杂、致密性要求高的零部件产品。
压铸生产要求零件尽可能壁厚均匀,以保证压铸冷却时尽可能同时凝固,但当零件壁厚差别较大时,就会在铸件厚壁处出现内部缩孔现象。为消除压铸件出现缩孔缺陷造成产品泄漏现象,一般采用局部挤压技术解决铸件缺陷。发动机前罩壳是汽车发动机的关键零件,用于密封发动机油道传输,对零件内部致密性要求非常高,内部各通油管道不得有泄漏串油现象。
1.前罩壳概述
前罩壳质量为3.6 kg, 材质为ADC12合金。外形尺寸为606.2 mm×351.4 mm×20 mm,平均壁厚为3 mm,模具型腔为一模一腔,产品壁厚不均匀。要求加工后采用气密测试, 0.3 MPa下油道之间不允许泄漏;该铸件属于密封性零件,壁厚不均匀,模具结构设计2组抽芯,采用油缸驱动滑块,单侧进料方式,分多股分支进料平步推进,有利于型腔填充成形,减少铸件气孔。压铸机采用意德拉22 000 kN,铸造压力选90 MPa,冲头直径为120 mm,内浇口速度为60 m/s。
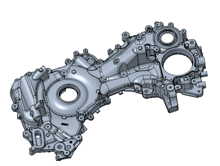
经过机加工后进行泄漏试验,发现在两个油道孔之间存在泄漏,产品合格率为20%,对产品进行剖切,发现油道间较大的缩孔是导致产品泄漏的主要原因。剖切图片见图2。
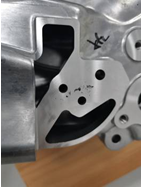
2 缺陷分析及解决措施
因泄漏位置为动模侧两支油道之间,且此位置壁厚较厚,且不均匀,油道孔径比较小(Φ6 mm),内部易产生缩孔。在油道孔对面静模侧有Φ16 mm斜抽芯孔,和油道孔之间壁厚较大,通过对斜抽芯孔型芯进行改造,将抽芯改为抽芯加挤压,可以大面积补缩到油道孔内部缩孔部位,增大油道孔之间的致密度。
通常局部挤压功能都是分布在动、静模方向,和压铸机开模方向一致,挤压销在开模后任意时刻进行抽插动作。本课题局部挤压在侧面斜滑块方向,在机床开模前挤压销必须完全退回离开铸件,否则会造成开模后挤压销拉断铸件,且在生产过程中若出现退出卡顿,不完全退出时也会造成铸件拉裂。为防止挤压销在移动过程中和销套之间出现卡顿,增加插芯喷涂功能,开模喷涂时需要将挤压销从底部位置再次顶出到位,接受喷涂润滑,增加挤压销的润滑性。随后,挤压销再次退回到底等待合模压射。鉴于以上生产风险和插芯喷涂功能要求,局部挤压采用抽芯加挤压结构,在开模取出铸件后,由喷涂机器人控制挤压销油缸顶出到位信号,在喷涂时驱动油缸顶出,实现插芯喷涂功能。在压射挤压后由压铸机控制挤压销油缸退出,若挤压销不能退位到底,机床抽芯信号报警,防止强制开模拉裂产品。
由于挤压销位置的特殊性,其退到位时端面和产品端面齐平,压射时直接挤压铸件底孔,具体结构形式见图3。可以看到,此种加压方式为挤压销直接挤压铸件孔,避免铝液和挤压销接触,不会出现铝液进入挤压销套内将其卡死或者磨损。并且挤压销在喷涂时伸出,得到定点喷涂的润滑,大大减少了挤压销和销套之间的摩擦。此外,在销子上做出油槽涂润滑脂,保障了局部加压连续生产。
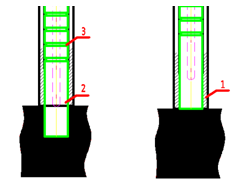
挤压销和销套之间的公差配合间隙直接影响生产连续性和挤压销的使用寿命。一般情况下,挤压销和销套配合公差越大,间隙越大,挤压销套内容易进入铝液卡死。模具挤压销公称尺寸为φ15 mm,和挤压销之间间隙为0.05~0.11 mm。
3 生产验证
3.1 挤压参数调试
在挤压生产时根据增压信号设定延时挤压时间和保压时间,在调试生产时通过设定不同的挤压延时和保压时间验证获得最佳外部和内部品质,见表1。
表1 挤压时间和保压时间设定

经不同组合参数调试验证,发现第4组参数下压铸的产品外观品质最优,生产最稳定,生产出的产品见图4。
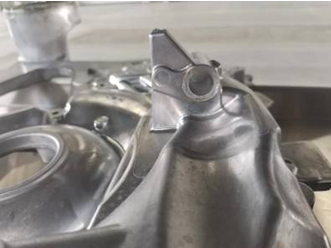
3.2 内部质量和试泄漏
将第4组参数生产的铸件经加工试密封试验后没有出现泄漏现象,并将铸件切开后,毛坯内部没有缩孔(见图5),挤压效果理想。
在调试生产过程中,静模滑块挤压效果满足预期设计目的,经过批量生产加工及密封验证后,产品的合格率为99%。
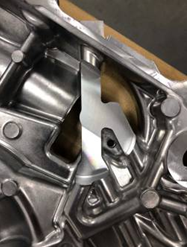
4 结语
此次抽芯加挤压并联动插芯喷涂技术,结合机器人喷涂信号驱动,实现了斜滑块局部挤压功能,大大改善了铸件内部质量。随着铸件结构越来越复杂,壁厚越来越不均匀,内部致密性要求也越来越高。
图文源:特种铸造
【本文引用格式】:刘鹏,李远超,柯旅,等.压铸前罩壳中缩孔缺陷解决措施[J].特种铸造及有色合金,2021,41(3):386-388.
免责声明:本图文来源于特种铸造,转载出于传递更多信息和学习目的,如转载内容涉及版权等问题,请立即联系小编,小编会予以更改或删除相关内容,以保证您的相关权益